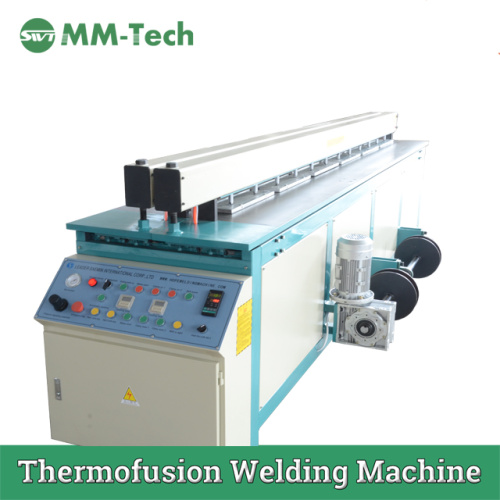
SWT-PH2000 Plastic Sheet Bending Welder
- Payment Type:
- L/C, T/T, D/P, Paypal, Money Gram, Western Union
- Incoterm:
- FOB, CFR, CIF
- Min. Order:
- 1 Set/Sets
- Min. Order:
- 1 Set/Sets
- Delivery Time:
- 7 Days
- Transportation:
- Ocean, Land
- Port:
- Qingdao, Shanghai, Tianjin
Your message must be between 20 to 2000 characters
Contact NowPlace of Origin: | Hebei,China |
---|---|
Productivity: | 2000set |
Supply Ability: | 20sets/Month |
Payment Type: | L/C,T/T,D/P,Paypal,Money Gram,Western Union |
Incoterm: | FOB,CFR,CIF |
Certificate: | ISO,CE |
HS Code: | 85158090 |
Transportation: | Ocean,Land |
Port: | Qingdao,Shanghai,Tianjin |
SWT-PH3000 Sheet Butt Fusion Welding Equipment
MM-Tech Thermoplastic Weld Machines included CNC Butt Fusion Welding Machine,Sheet Butt Fusion Welding Equipment,Themoplastic Sheet Butt Fusion,and the overall machine concept creates the ideal requirements for quality-assured welding in accordance with DVS 2208-1.
The PVC,PE Board Butt Fusion Machines is accurate, efficient & easy-to-use, and can be used to weld in horizontal and circular butt fusion.
PVC Sheet Welding Machines Feature
1.The electric system is placed in electric cabinet concentratedly, so it's convenient for maintenance and check.
2.Press button control makes the operation easy and convenient.
3.The working panel's material is Q345 manganese, which's featured as non-being heated distortion; The platen's material is aluminum, and for each platen there're two air cylinders providing the power, ensuring the compressive stress is very strong.
4.The heating pipe is inserted through the heating knife, so it's easy and convenient to replace the heating elements. The material of heating knife is imported grade aluminum, with teflon coated. It has the advantage of non-being heated distortion and non-stick.
5.Specially designed rolling device makes the rolling work easy and labor saving.
6.Specially designed LED lights can make you observe the process of welding clearly.
PP Sheet Welding Machines Technical Specifications
Specification/Size | SWT-PH2000 | SWT-PH3000 | SWT-PH4000 | SWT-PH5000 | SWT-PH6000 |
Weldable sheet thickness (mm) |
3.0-30.0 | 3.0-30.0 | 3.0-30.0 | 3.0-30.0 | 3.0-30.0 |
Max.working length (mm) |
2000 | 3000 | 4000 | 5000 | 6000 |
Roll circle min diameter (mm) |
380 | 400 | 450 | 550 | 550 |
Air pressure (kg.f /cm2) |
4.0-8.0 | 4.0-8.0 | 6.0-8.0 | 6.0-8.0 | 6.0-8.0 |
Energy source (m3/min) |
0.0032 | 0.0052 | 0.0062 | 0.0068 | 0.0075 |
The rated voltage (V) |
380 | 380 | 380 | 380 | 380 |
Rated current (A) |
9 | 13.6 | 13.6 | 13.6 | 13.6 |
Heating Power (KW) |
4kw | 6kw | 8kw | 10kw | 12kw |
Power of Rolling Motor (KW) |
1.5kw | 1.5kw | 1.5kw | 1.5kw | 1.5kw |
Heating mode | Overall heating | Overall heating | Overall heating | Overall heating | Overall heating |
Drum institutions(parts) | Optional | Optional | Optional | Optional | Optional |
External dimensions (L*W*H) mm |
2800*1200*1200 | 3750*1200*1200 | 4850*1200*1200 | 5850*1200*1200 | 6900*1200*1200 |
Packing dimensions (L*W*H) mm |
3000*1300*1450 | 3900*1300*1450 | 5000*1300*1450 | 6000*1300*1450 | 7050*1300*1450 |
N.W KGS | 850kg | 1350kg | 1550kg | 1800kg | 1900kg |
G.W KGS | 1000kg | 1500kg | 1700kg | 1950kg | 2100kg |
Heating element: Heating Plate was coated with Teflon. | |||||
Device equipped with automatic winding device mechanism | |||||
Suitable material: PP, PE, PVDF, PVC, PPN, etc. | |||||
Can be customized according to customer requirements | |||||
Scope of application: electroplating equipment, environmental protection equipment,chemical containers, sewage treatment, piping, ventilation systems and other industries |
Themoplastic Sheet Butt Fusion Application
Butt fusion, also referred to as heated element welding or heated element butt welding, is a widely used technology. The fusion method is used in high volume production applications of molded parts as well as in the field of thermoplastic piping and sheet products. The butt fusion method generally provides a very high quality weld when the material`s specific parameters are adhered to. In principle, the process requires that the materials to be welded are held against a heated plate, the heated plate is removed and the materials are pressed together. The parameters that need to be observed are time, temperature and pressure. These vary depending on type of material and size of weld surface. A graph (Figure 1) explains the process as follows:
The high pressure melting cycle assures that a bead is formed all along the heater plate to guarantee material contact to the element.
The low pressure heating cycle permits the heat to be absorbed into the material.
The change over time, i.e. the time it takes for the element to be removed and to bring the two materials into contact with each other, needs to be kept to a minimum to avoid cooling or even oxidation of the surfaces to be welded.
The welding time allows the material to cool down under pressure to form the appropriate molecular bond. An important step here is the [Pressure built-up time," which should be performed as a ramp, rather than smashing the materials together and squeezing the heated molecules out of the weld zone.
Machine Requirements
The German Welding Society (DVS) has comprehensive guidelines for this process and materials and DVS 2208- 1, in particular, spells out in detail the requirements for butt welding machines for both piping and sheet. A few of these cover:
Machine frame, construction and guide/travel elements.
Material clamping fixtures and their impact on machine base.
Machine table travel parallelism and table top alignment.
Heating element positioning, temperature accuracy and surface condition.
Machine controls
Related Keywords